Silicone Tubing Supplier & Manufacturer in China
Tenchy specializes in manufacturing high-quality silicone tubing, particularly platinum-cured silicone tubing, known for its exceptional purity and durability. The platinum curing process results in silicone rubber tubing with superior flexibility, high-temperature resistance, and excellent chemical resistance. Our silicone tubing comes in a wide range of sizes, wall thicknesses, and colors, customizable for diverse application needs. Whether you require silicone tubing for medical devices, food processing, or demanding industrial applications, Tenchy offers reliable, customizable solutions.
- Durable and Flexible: Available in durometers 30-80 Shore A for varied applications.
- Extreme Temperature Resistance: Withstands temperatures from -60°C to 220°C.
- Food and Medical Grade: Complies with FDA and USP Class VI standards for safety.
- Customizable: Available in various sizes, wall thicknesses, and colors to meet specific needs.
- Kink-Resistant: Maintains its shape even under pressure, ideal for smooth fluid transfer.
- Chemically Resistant: Resistant to mild acids, bases, solvents, and oxidation.
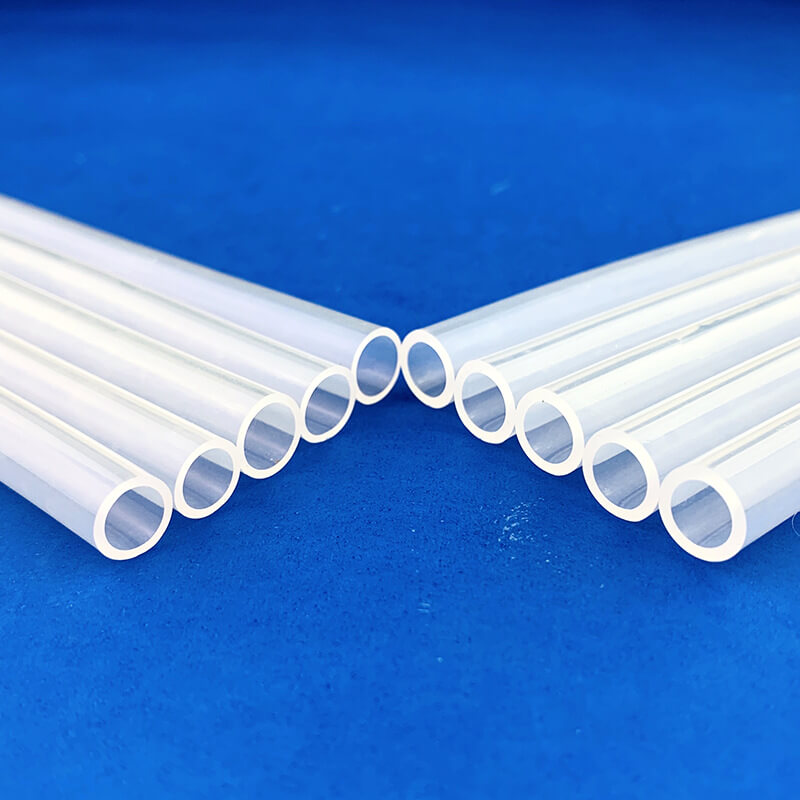
Silicone Tube Types
Tenchy offers silicone tubing in various types, tailored to meet industry-specific demands:
- Food grade silicone tubing for food and beverage processing
- Medical grade silicone tubing for critical healthcare applications
- High temp silicone hose for industrial use
- Customized silicone hose and tube of silicone options to fit unique requirements
- Thin wall silicone tubing and clear silicone tubing for precise applications
For specialized uses, we provide silicone rubber insulation tube for power cables in the electrical sector, conductive silicone tube & sheet for electromagnetic shielding applications, and reusable food-grade silicone drinking straws for environmentally friendly consumer products. our silicone heat shrink tubing also performs exceptionally in protecting and insulating components in demanding environments.
Tenchy’s silicone tubing boasts exceptional flexibility, allowing it to bend without damage, making it perfect for tight spaces. Its inherent durability ensures a long service life, reducing the need for replacements. The silicone tubing’s resistance to high temperatures and harsh chemicals guarantees it remains intact in challenging environments.
Our silicone tubing can withstand extreme high and low temperatures without compromising its structural integrity. It is resistant to UV radiation, moisture, and ozone, ensuring long-lasting performance in harsh conditions. For extreme heat applications, choose Tenchy’s high temperature silicone tubing, ideal for systems requiring superior heat and chemical resilience.
Our silicone tubing is biocompatible, meaning it can handle sensitive biological fluids without triggering immune responses. It can be sterilized through various methods such as autoclaving, irradiation, or ethylene oxide, making it perfect for use in medical devices where hygiene is critical.
Tenchy’s silicone tubing is not only a high-performance material but also comes with premium packing and shipping, ensuring it arrives in optimal condition and ready for use.
Why Choose Tenchy's Silicon Tubing?
Silicone tubing is a versatile and resilient solution for various industries, from healthcare to aerospace. Its high-temperature resistance, chemical compatibility, and biocompatibility make it an excellent choice for medical grade silicone tubing as well as industrial applications. Whether you’re looking for silicone tubing manufacturers or bioprocess silicone tubing, Tenchy is your trusted partner.
Request a quote today for competitive silicone tube prices tailored to your specific order volume and requirements.
Silicone Hose Parameters
Production Process | Silicone Extrusion |
Density | 1.10-1.20g/cm³ |
Hardness | 30 Shore A-80 Shore A |
Temperature Resistance | -60℃-220℃ |
Standard | RoHS, ISO, REACH, FDA, LFGB |
Tensile Strength | ≥10.1MPa |
Elongation at Break | ≥470% |
Tensile Set | 12% |
Compression Set | 8% |
Tear Strength | ≥25 KN/m |
Working Pressure | 0.8 bar-26.0 bar |
Burst Pressure | 2.4 bar-78.0 bar |
Weather Resistance | Durability, UV Resistance |
Temperature Resistance | |
Moisture Resistance | |
Chemical Resistance | Mild Acids and Hases Resistance |
Solvents Resistance | |
Oxidation Resistance | |
Oil Resistance | Oil Resistance |
Hydrocarbon Exposure Resistance | |
Plasticizers and Lubricants Resistance | |
Water Absorption | Low Water Absorption(<1%) |
High Hydrophobic Nature | |
Cured Method | Platinum Cured |
Silicone Tubes Applications
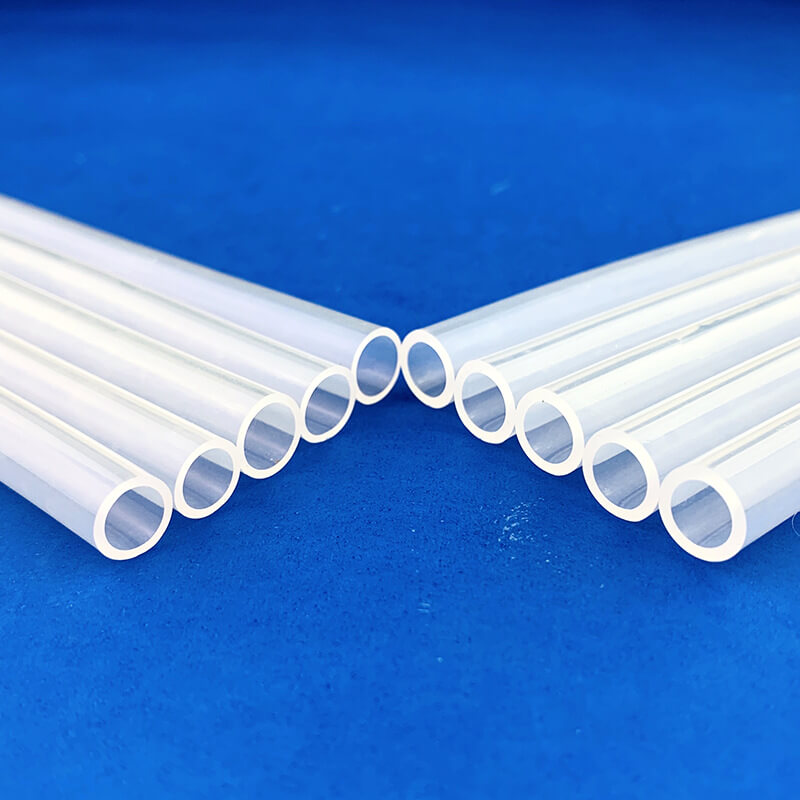
Healthcare and Life Sciences
Silicone tubing is a critical component in medical devices such as catheters and infusion sets. Its biocompatibility ensures patient safety and fluid purity. Sterilizability guarantees it meets stringent healthcare standards, offering a reliable solution for sensitive medical environments.
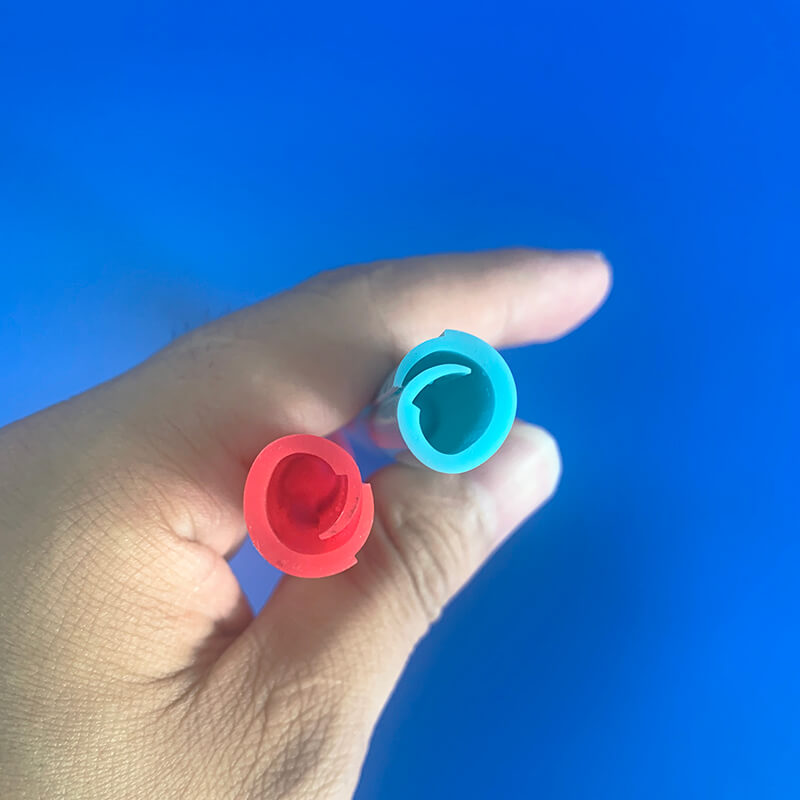
Food and Beverage Processing
Our food-grade silicone tubing meets the strictest health standards, ensuring safe fluid transfer without affecting the quality of food or beverages. Its non-reactive nature ensures product purity during the processing stages.
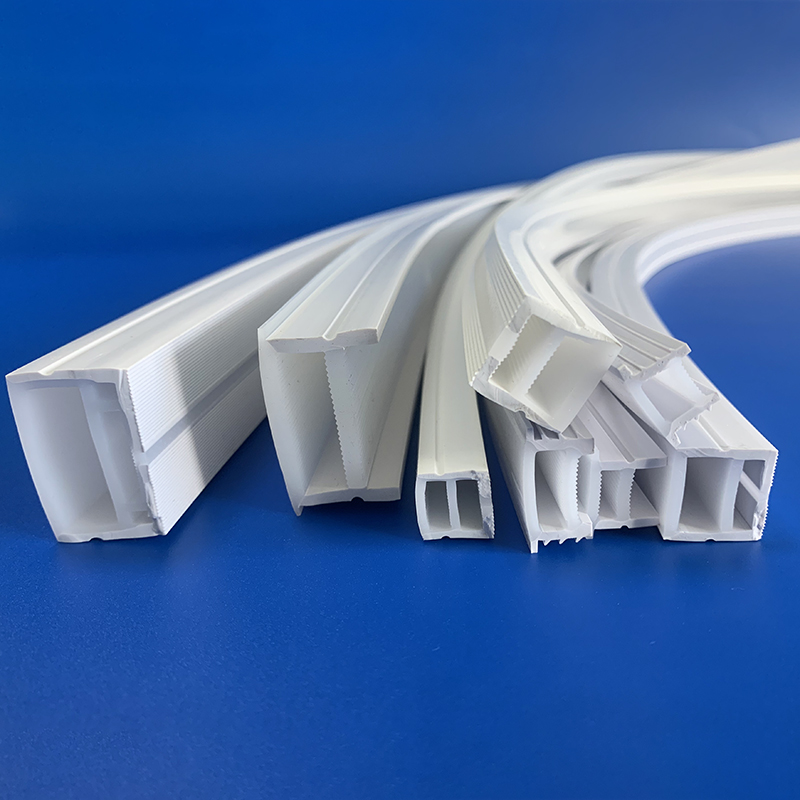
Industrial and Manufacturing Processes
Our silicone tubing excels in industrial settings due to its chemical resistance and ability to handle extreme temperatures. It is commonly used for fluid transfer and protective coverings in equipment, contributing to efficiency by reducing downtime and maintenance needs.
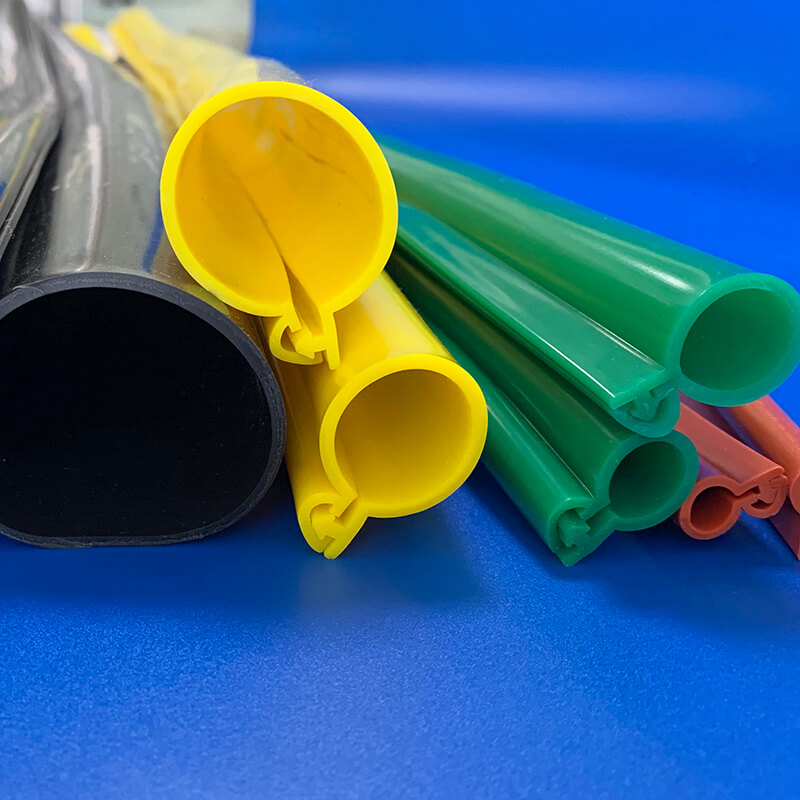
Specialized Applications
Tenchy offers custom solutions for specialized industries, including automotive, aerospace, and scientific research. Our heat proof silicone tubing withstands extreme heat, while flexible silicone tubing ensures adaptability in various applications.
More Information
Silicone Tubing Usage Methods
- Cutting to Desired Length
Silicone tubing can be cut to desired lengths to suit specific requirements. The cutting process must be clean and accurate to ensure a proper fit with other components and to maintain the tubing’s performance characteristics without causing damage or deformation.
- Connecting to Fittings
Connecting tubing to fittings requires careful attention to ensure a secure and leak-free connection. The tubing should be matched with compatible fittings and firmly attached to prevent disconnection or bypass, which could compromise the system’s functionality.
- Securing with Clamps or Fasteners
Once connected, the tube is often secured using clamps or fasteners to reduce the risk of detachment or leakage under pressure. Selecting the appropriate securing method is crucial to maintain the integrity of the connection during operation.
- Insertion into Equipment or Systems
Silicone tubing must be inserted into equipment or systems with care to prevent kinks or damage. Proper insertion ensures the tubing functions correctly, providing a reliable conduit for fluids or gasses within the equipment or system.
- Testing for Leaks
After installation, it should be tested for leaks to guarantee airtight and fluid-tight seals. This step is vital to ensure safety and efficiency, particularly in applications where the integrity of the conveyed material is critical.
- Replacing and Reinstallation
Over time, silicone tubing may need to be replaced to maintain optimal performance. The reinstallation process involves removing the old tubing, preparing the new tubing, and ensuring it is installed correctly to meet the application’s requirements.
Silicone Tubing Care & Maintenance
Proper care and maintenance of such tubes are essential for its longevity. Regular cleaning, proper storage, and routine inspections are necessary to maintain the tubing’s integrity. Adherence to recommended maintenance schedules can significantly extend the life of silicone tubing in any application.
- Cleaning
Cleaning silicone tubing involves flushing it with appropriate solvents to remove residues and contaminants. It’s important to select cleaning agents compatible with silicone to prevent degradation. Regular cleaning maintains the tubing’s performance and prevents buildup that might impede flow or cause contamination.
- Storage
The tubing should be stored in a cool, dry place away from direct sunlight to prevent premature aging. Keeping the tubing away from sharp objects and chemicals that can cause damage ensures it remains in optimal condition until its next use.
- Sterilization
Sterilization procedures for them must adhere to specific protocols to achieve the required level of cleanliness and sterility. These procedures are essential in applications where hygiene and the absence of contaminants are non-negotiable.
- Safety Measures
Safety measures for tubes of silicone include proper installation, avoiding extreme temperatures, and compatibility checks. Adhering to these guidelines ensures safe operation and prevents accidents. These measures contribute to a safe working environment and prolong the service life of the tubing.
- Proper Installation
Proper installation of silicone tubing is crucial for its effective operation. It involves ensuring a secure fit with fittings and clamps, avoiding kinks or twists that can impede flow. Correct installation prevents leaks and potential failures that could lead to safety hazards or system downtime.
- Avoiding Extreme Temperatures
Silicone tubing should be operated within its specified temperature range. Exposure to temperatures beyond its tolerance can lead to degradation, affecting its performance and safety. Users must be mindful of the operating environment to maintain the tubing’s integrity.
- Compatibility Check
It’s important to conduct compatibility checks for silicone tube with the chemicals or fluids it will be exposed to. Incompatible substances can cause the tubing to swell, become brittle, or even fail. Ensuring compatibility helps prevent accidents and maintains the quality of the transported media.
- Regular Inspection
Regular inspection of silicone tubing is necessary to detect signs of wear, damage, or aging. Identifying issues early allows for timely repairs or replacements. Inspections contribute to the reliability of systems that rely on silicone tubing and prevent unexpected failures.
FAQs
1. What temperature range can silicone tubing withstand?
Silicone tubing can typically handle temperatures ranging from -60°C to 200°C (-76°F to 392°F).
2. Is silicone tubing safe for medical and food applications?
Silicone tubing is FDA-approved for medical and food contact use due to its biocompatibility and inert nature.
3. Can silicone tubing be sterilized?
Silicone tubing can be autoclaved, gamma irradiated, or sterilized using ethylene oxide (EtO) methods.
4. Does silicone tubing react with common chemicals?
Silicone tubing is resistant to many chemicals, but it’s important to check compatibility with specific substances.
5. How flexible is silicone tubing?
Silicone tubing is highly flexible, making it suitable for various bending and routing applications.